I developed an interest in St Alban’s Abbey LNWR station back in 1998 when a mate and I first started kicking the ideas around about an exhibition layout. Whilst my current incarnation is a “based on” rather than an accurate model, I have long harboured the desire to build a more accurate model, using the correct buildings, track plan and rolling stock. I have had plans for the station building for some years but have never managed to get around to building it. A friend built a model of the good shed for me back when we first exhibited the layout but it was a bit over scale and built from fairly thick card so wasn’t really suitable. Additionally, whilst it was built in brick (well brick paper) – which in itself was outside normal LNWR practice of wooden sheds – the colour chosen was red, where as I have since learned the buildings at St Alban’s were built out of a yellow shade.
Fast forward to 2014 and I have become a Tech Drawing teacher with access to a CAD program and my thoughts turned to drawing the building from the plans I had and getting it printed. Whilst this was going on, I obtained a copy of LNWR Portrayed by Jack Nelson and wonders of wonders, it had the plans of the St Alban’s Abbey Good Shed in it. I assume Rodger had a copy of the same book back in the late 90s – can’t ask him, he returned to the UK some years ago and we lost touch. Anyway, the idea of printing a building continued and I drew up the Goods Shed and uploaded the file to Shapeways to see what it would cost – and I wasn’t impressed! Allowing for the various “free postage” deals Shapeways offers from time to time it still wasn’t a price I considered worth paying so there it stayed.
We got a printer at work last year and I looked into it again – but decided that 9 hours of printing was going to be a bit hard to hide from the power that be and in any case, I wasn’t too impressed with the quality of prints. As it happens, I have learnt how to drive that particular printer better since and had a rethink on how I was going to finish the building but even so, the length of the print time for a private venture wasn’t going to endear me to anyone.
As I mentioned in my Update in April, I purchased a printer from one of the local Aldi stores when they were selling them in February. A few test prints later, and I was ready to try producing the Goods Shed.
The first print was of the square base. In fact, I printed this upside down as I had learnt that doing it the other way was likely to cause issues with the door ways – the printers don’t like trying to print over thin air.
By printing it upside down the door ways were fairly clean and only require a little bit of cleaning up with knife, file and sand paper. (LNWR D88 from the 2mm Scale Association in the railway door on the office side – office not yet printed at this point.)

The next print was the office on the buffer stop side of the Shed. This was printed correct way up as the angles for the roof needed to be included. I decided to print the steps at this stage because I thought it would be easier to draw it than file a block to fit. The office window was included as I was interested to see how the arch would go – and it went much better than I expected to be honest. I suspect the stepping process (I print at 0.08mm and so each layer can build on the next so long as it isn’t too shallow an angle) worked ok where as trying to do 90° wouldn’t work. I glued the office bit to the main bit with super glue. I print with PLA plastic (that’s what came with the printer – other options are available, one which apparently will respond to plastic weld) and my normal glues wouldn’t touch it.
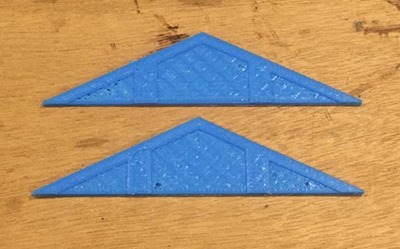
Having done so well with the original prints, I next drew up the gable ends and printed them. I had tinkered with the settings on these and the result was as seen above. On investigation I had made the top layer too thin – as mentioned, I print a 0.08 layer and tried printing only a couple of layers for the final layer and they sagged into the fill. Changing the setting to make a 0.4mm thick layer meant it was much better the second time. The gables were likewise fitted with super glue.
Lastly I drew up and printed the interior platform. I again drew the two sets of stairs and left a gap around the whole to allow for interior decorating.
The next step involved sorting a roof and then dealing with the blue. The roof was done with a couple of sheets of 0.5 plasticard and the bricks were sourced from Scalescenes (their London Brick option for the Scratch Builders Yard). As my wife is into paper crafts and scrapbooking, she has a large range of suitable tools for working with paper so one evening while she was out I availed myself of them. She also has a collection of inks for stamping designs and one of them was a good match for blending in the cut edges. The slate roof came from Shapeways too. D15 Shapeways print lurking in the doorway this time.
Lighting on the Shed was principally supplied by two massive sky lights as fars and the drawings and indistinct pictures show. So I drew where they were to go on the roof then cut out the rectangle with a slitting disc in my trusty Dremel. A piece of OHT was slipped under the tile paper and then various sizes of plastic strip were used to put the framing on.
Annoyingly leaking plastic weld discoloured the print – I hadn’t sealed it yet and paid the price however I am not sure that I could have glued it all had I sprayed clear varnish over it all. In the end I glued a second sheet of tile paper over it and this had the unexpected bonus of helping to blend the framing in.
After both sides were done, I painted the bars grey. There is still some work to do but overall it looks pretty good.
I noticed after I took this that I need to get the blending ink out again – not sure how I missed that!!
The corner has been reglued with PVA – using a UHU glue stick clearly wasn’t a good idea as this wasn’t the only bit which lifted. It is also obvious that I haven’t done the inside walls yet. They are going to end up painted bricks.
So pretty pleased with progress. I still have to put the boards on the gable ends, fit gutters and down pipes, sort out the stairs, door and window and then weather it all. While there are those two big sky lights and I am therefore going to have to detail the interior more than I had originally thought, I don’t imagine they were cleaned that regularly!